HYDRAULIC POWER & CONTROL UNIT (HPCU)
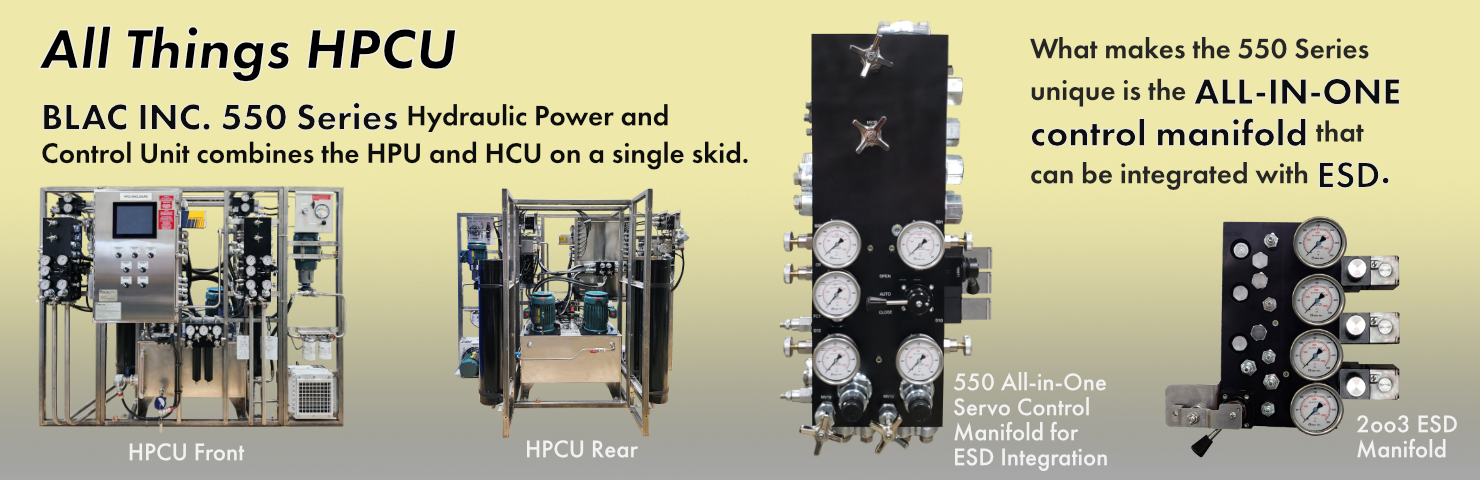
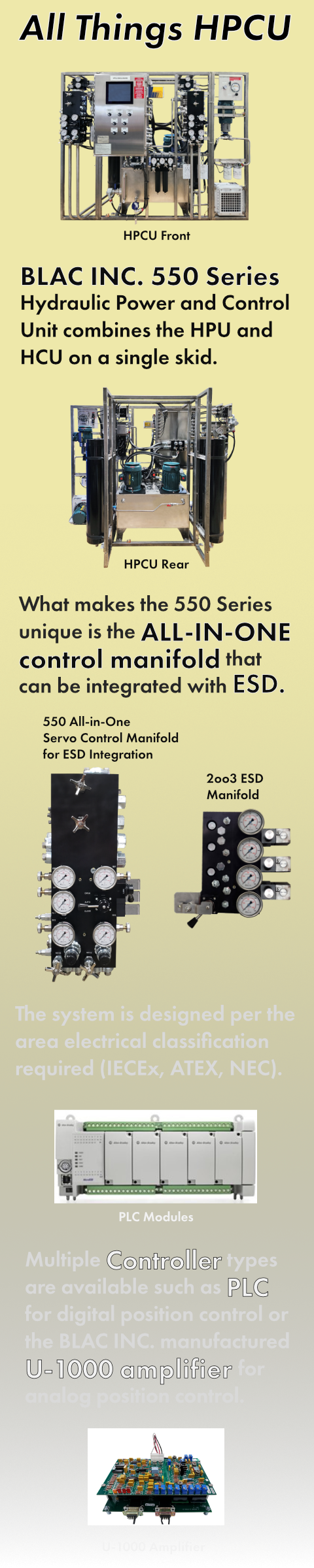
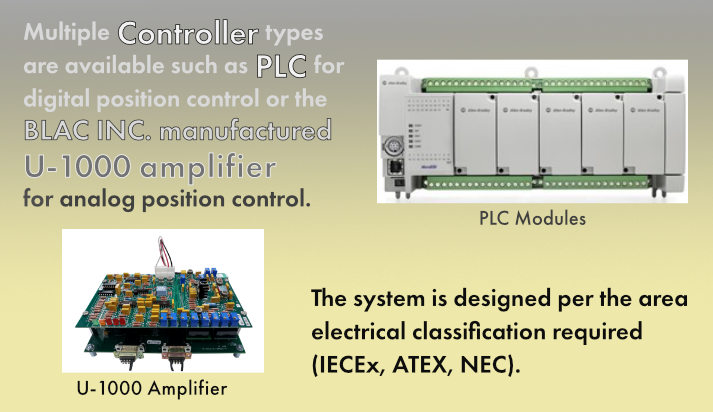
Hydraulic Power Unit (HPU)
Tap on the image of the HPCU skid to highlight the HPU section. Tap outside of the image to return to full HPCU skid view.
Hover on the image of the HPCU skid to highlight the HPU section.

HPU Summary
The Hydraulic Power Unit supplies high pressure hydraulic fluid to operate one or more valves.
The HPU contains the hydraulic fluid reservoir and two main oil supply pumps that provide the high pressure fluid to the Hydraulic Control Unit (HCU).
The oil is filtered through either of two filters that may be operated with either of the two main pumps.
A third pump may be used in an optional circulation system to continuously move fluid through an additional set of filters prior to fluid returning to the reservoir.
HPU Components
The HPU section of the HPCU consists of the following main components:
Hydraulic Control Unit (HCU)
Tap on the image of the HPCU skid to highlight the HCU section. Tap outside of the image to return to full HPCU skid view.
Hover on the image of the HPCU skid to highlight the HCU section.

HCU Summary
The Hydraulic Control Unit receives the high pressure fluid from the Hydraulic Power Unit (HPU) and performs the control functions necessary to operate the hydraulic cylinder(s) that move the final control element.
The HCU provides the control functions for the valve actuator including automatic operation from the BPCS/DCS command signals with normal positioning by servo control. A fail in position (lock-in-place) function isolates the servo when certain failures occur to keep the valve from moving.
The main accumulator acts to store power in case of pump/motor failure to provide the immediate fluid volume required for valve movement. An additional ESD accumulator is provided for systems requiring an emergency shutdown function.
Manual directional control via hand valves, handwheel usage, and remote positioning by jog solenoid valves are among the other methods of moving the valve.
HCU Components
The HCU section of the HPCU consists of the following main components:
HPCU Controller Enclosure
Tap on the image of the HPCU skid to highlight the HPCU Control Enclosure section. Tap outside of the image to return to full HPCU skid view.
Hover on the image of the HPCU skid to highlight the HPCU Controller Enclosure section.

HPCU Controller Enclosure Summary
The electronic terminations of the valve control system are located inside the HPCU Controller Enclosure mounted to the HPCU skid.
The enclosure is designed to meet hazardous area classification and when required uses a “Z” purge assembly.
PLC-based position control may be implemented with any of several customer preferred PLC vendor options available. Analog-based systems use the BLAC INC. U-1000 amplifier for analog position control.
There are options for a local HMI with touchscreen or pushbutton screen selector, or may use process meter displays for position command and feedback.
Redundant power supplies provided along with enclosure heater, vortex cooler or air conditioning unit depending on ambient conditions.
Hand switches on the front panel of enclosure for pump operation, cooling system and reservoir heater operation, and feedback device selection as required.
HPCU Controller Enclosure Components
The HPCU Controller Enclosure section of the HPCU consists of the following main components:
Emergency Shutdown (ESD) Manifold
Tap on the image of the HPCU skid to highlight the ESD section (2oo2 ESD manifold is shown). Tap outside of the image to return to full HPCU skid view.
Hover on the image of the HPCU skid to highlight the ESD section (2oo2 ESD manifold is shown).

ESD Summary
For an in-depth look at the BLAC INC. emergency shutdown function logic for 2oo2 and 2oo3 voting systems along with Safety Integrity Level (SIL) discussion, see the BLAC INC. Technical page.
Overviews of the 2oo2 and 2oo3 ESD systems follow:
2oo2 ESD Summary
The emergency close signal is given by removing power from each of the two (2) solenoid valves. The system is designed to be fault-tolerant, and a failure of one (1) solenoid valve will not cause a nuisance shutdown.
The ESD Test hand valve allows the testing of one or both solenoids without moving the driven valve. The associated limit switch provides indication that the ESD system is out of its normal Auto operation.
2oo3 ESD Summary
The emergency close signal is given by removing power from the three (3) solenoid valves. The system is designed to be fault-tolerant, and a failure of one (1) of the solenoid valves will not cause a nuisance shutdown or prevent a demanded shutdown from occurring.
The 2oo3 manifold that contains the voting logic is tubed to the control manifold stack where the ESD logic valves reside. During an emergency shutdown the piloting pressure is drained from the ESD logic valves, causing them to move to their ESD state.
The ESD Test hand valve allows the testing of one (1), two (2) or all three (3) solenoids without moving the driven valve. The associated limit switch provides indication that the ESD system is out of its normal Auto operation.
Safety Integrity Level (SIL)
Many refiners request “SIL Rated” systems from FCCU actuator vendors. For emergency shutdown, the Safety Instrumented Function includes much more than only the ESD solenoids.
Refer to our Technical section on SIL for information on how BLAC INC. hired a third-party to perform Fault Tree Analysis on the entire system function to determine SIL.
ESD Manifolds
The following shows typical 2oo2 and 2oo3 ESD manifolds and their integration with the 550 Series servo control manifold or stacked control manifold designs:
550 Series HPCU Gallery
Various images of HPCU designs using the 550 All-in-One control manifold follow:
Options for single or dual (or more!) control manifolds on a single skid are just the beginning.
Choose PLC digital control with a local HMI or use the BLAC INC. U-1000 analog controller with command and feedback displays available to the local operator.
Add a circulation system for additional filtering and a cooling fan motor may be desirable for units in warm weather climates.
Typical ESD arrangements for 2oo2 or 2oo3 voting can be integrated as the service requires.
If you have a special requirement, BLAC INC. Engineering will work with you in designing the proper solution. Get started by contacting us.
Dual 550 Control Manifolds (each with 2oo2 ESD) using PLC & HMI, Circulation Pump & Fan Cooler
550 Series HPCU - Dual Control Manifolds & PLC/HMI, Circ Pump/Cooler (Front View)
550 Series HPCU - Dual Control Manifolds & PLC/HMI, Circ Pump/Cooler (Rear View)
Dual 550 Control Manifolds (each with 2oo2 ESD) using PLC & HMI, Circulation Pump
550 Series HPCU - Dual Control Manifolds & PLC/HMI, Circulation Pump (Front View)
550 Series HPCU - Dual Control Manifolds & PLC/HMI, Circulation Pump (Rear View)
Dual 550 Control Manifolds (each with 2oo2 ESD) using PLC & HMI
550 Series HPCU - Dual Control Manifolds & PLC/HMI (Front View)
550 Series HPCU - Dual Control Manifolds & PLC/HMI (Rear View)
Three (3) 550 Control Manifolds (one with 2oo3 ESD) with Displays for Command & Feedback
550 Series HPCU - Three (3) Control Manifolds, One (1) with 2oo3 ESD (Front View)
550 Series HPCU - Three (3) Control Manifolds, One (1) with 2oo3 ESD (Rear View)
Dual 550 Control Manifolds with Bottom Mount Motors (available upon request)
550 Series HPCU - Bottom Mount Motors Available Upon Request (Front View)
550 Series HPCU - Bottom Mount Motors Available Upon Request (Rear View)
Single 550 Control Manifold (no ESD) using U-1000 Analog Controller
550 Series HPCU – Single Control Manifold & U-1000 (Front View)
550 Series HPCU – Single Control Manifold & U-1000 (Rear View)
Dual 550 Control Manifolds (no ESD) using U-1000 Analog Controllers
550 Series HPCU – Dual Control Manifolds & U-1000 (Front View)
550 Series HPCU – Dual Control Manifolds & U-1000 (Rear View)